In vibration analysis, there is one significant element that is essential: the acceleration transducers or accelerometers. However, when it comes to obtaining the most reliable and accurate measurements, it is necessary to take into account aspects such as the choice of accelerometer suitable for the measurement to be made and the method of mounting.
Type of transducers
In general, transducers are elements that convert mechanical movements into electrical signals. An example application is available at https://www.cere.link/. They can be of three different types, depending on the quantity to be measured:
— Displacement transducers or proximity probes : used to measure the alignment of shafts in turbines, large pumps and centrifugal compressors, they are permanently mounted and are ideal for low speeds and low frequencies.
— Speed Transducers: They operate on the principle of electromagnetic induction and are used for machines with fault frequencies ranging from 10 Hz to 2000 Hz. They are larger than other types of transducers and are sensitive to magnetic and thermal fields.
—Acceleration transducers or accelerometers : These are the most widely used transducers because they cover a wide range of frequencies, maintain adequate accuracy at high temperatures and frequencies (5 Hz to 20 kHz) and withstand industrial conditions.
They consist of piezoelectric crystals that, when excited by the vibratory force, generate an electrical output signal directly proportional to the value of the vibratory acceleration. There are also specific accelerometers for special applications, such as those with high sensitivity, high temperatures or explosive atmospheres. It is even possible to take measurements in three directions from the same position with triaxial accelerometers.
Disadvantage
As a disadvantage, it should be noted that ICP (Integrated Circuit Piezoelectric) type accelerometers require an integrated signal amplifier circuit, which requires a stabilization time of several seconds before starting a measurement.
On the same subject
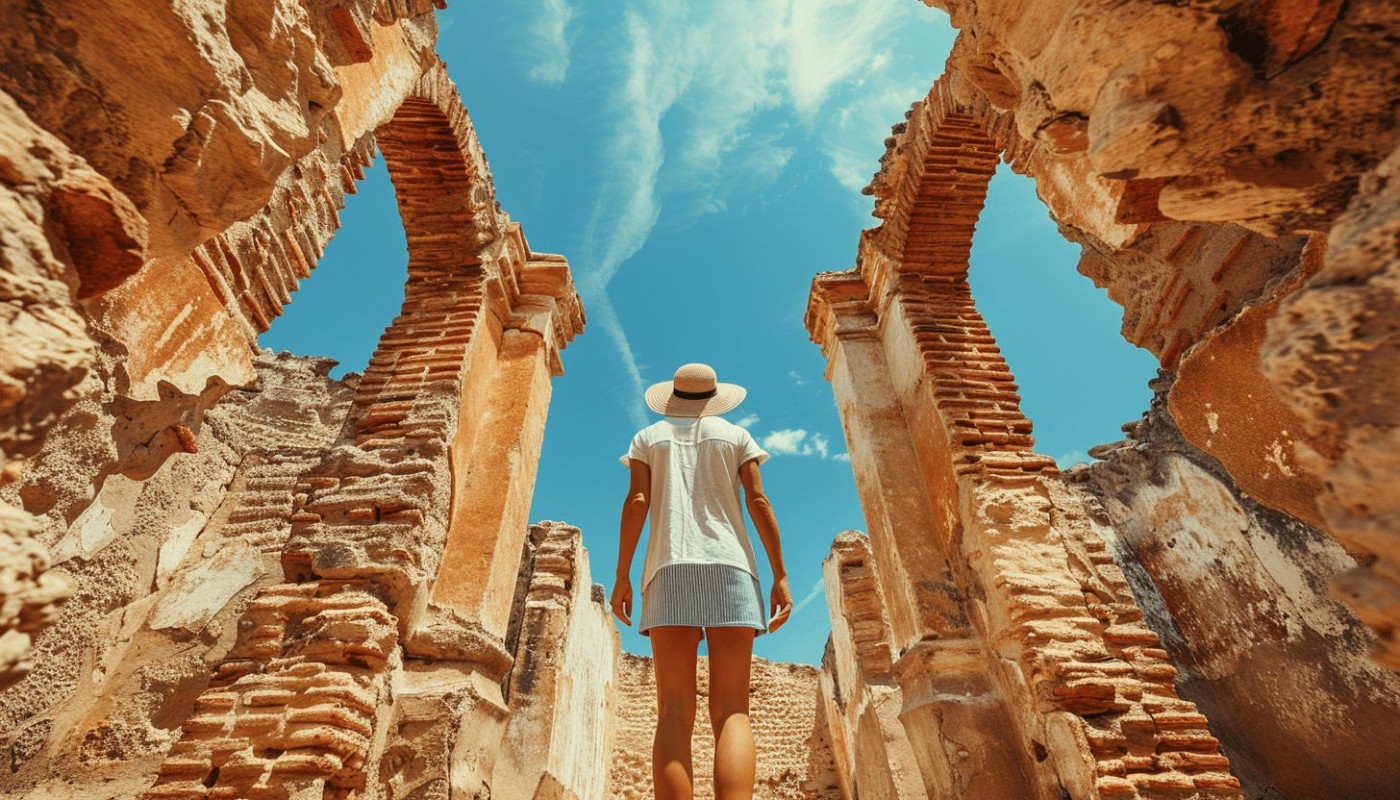
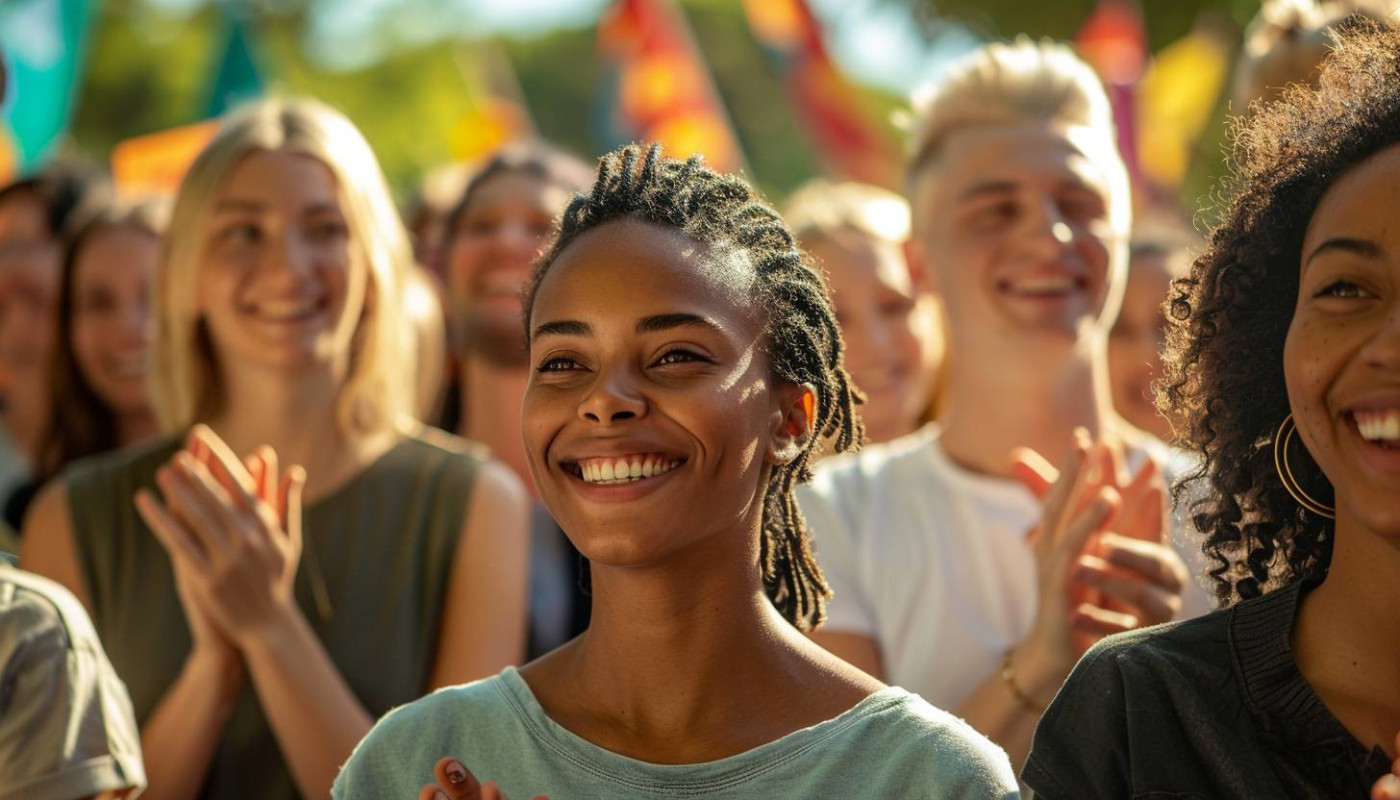
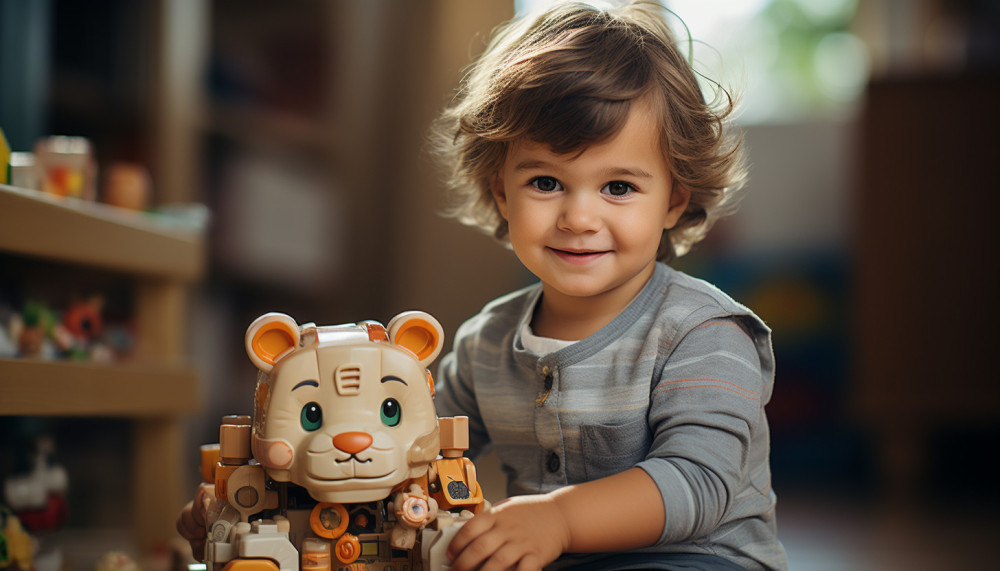
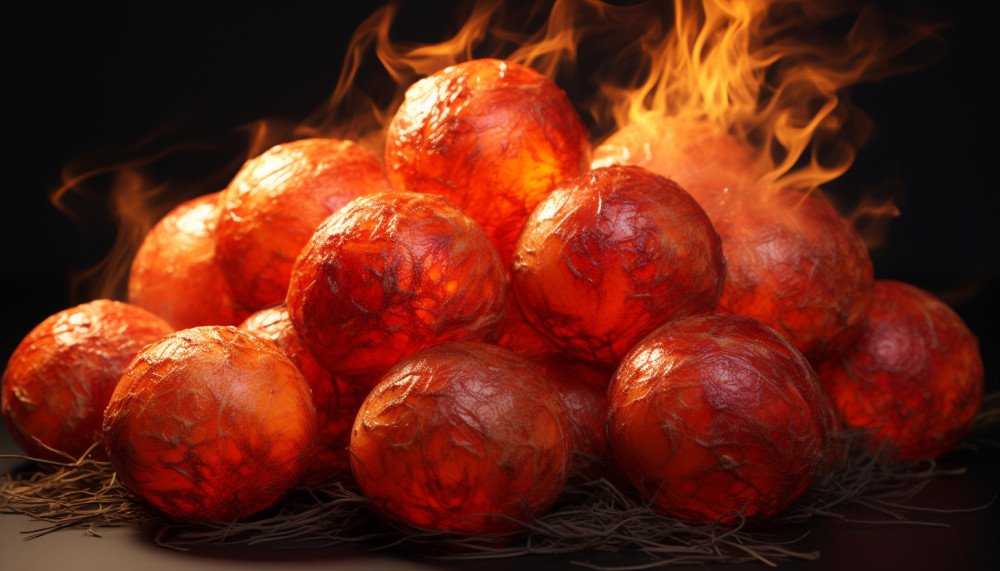
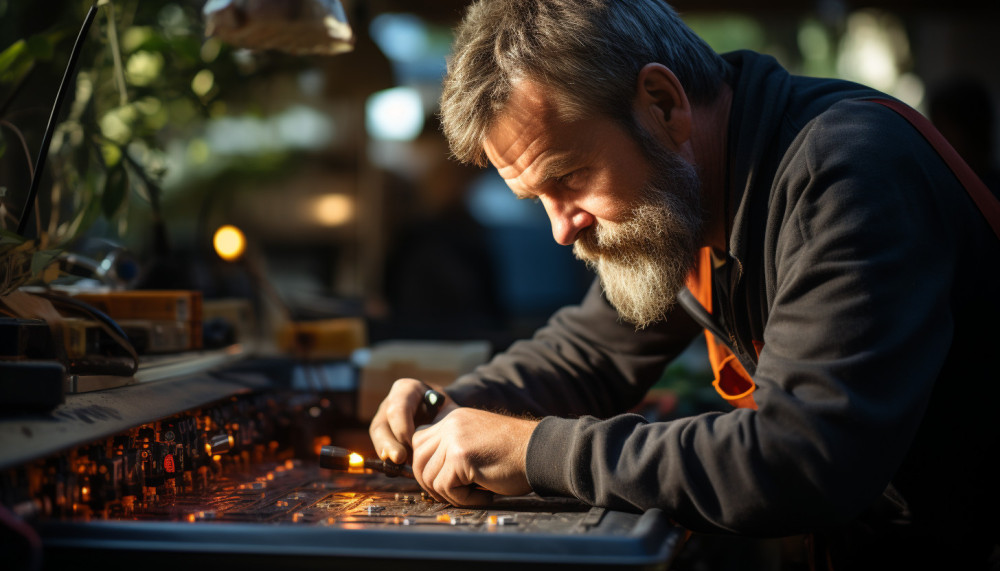
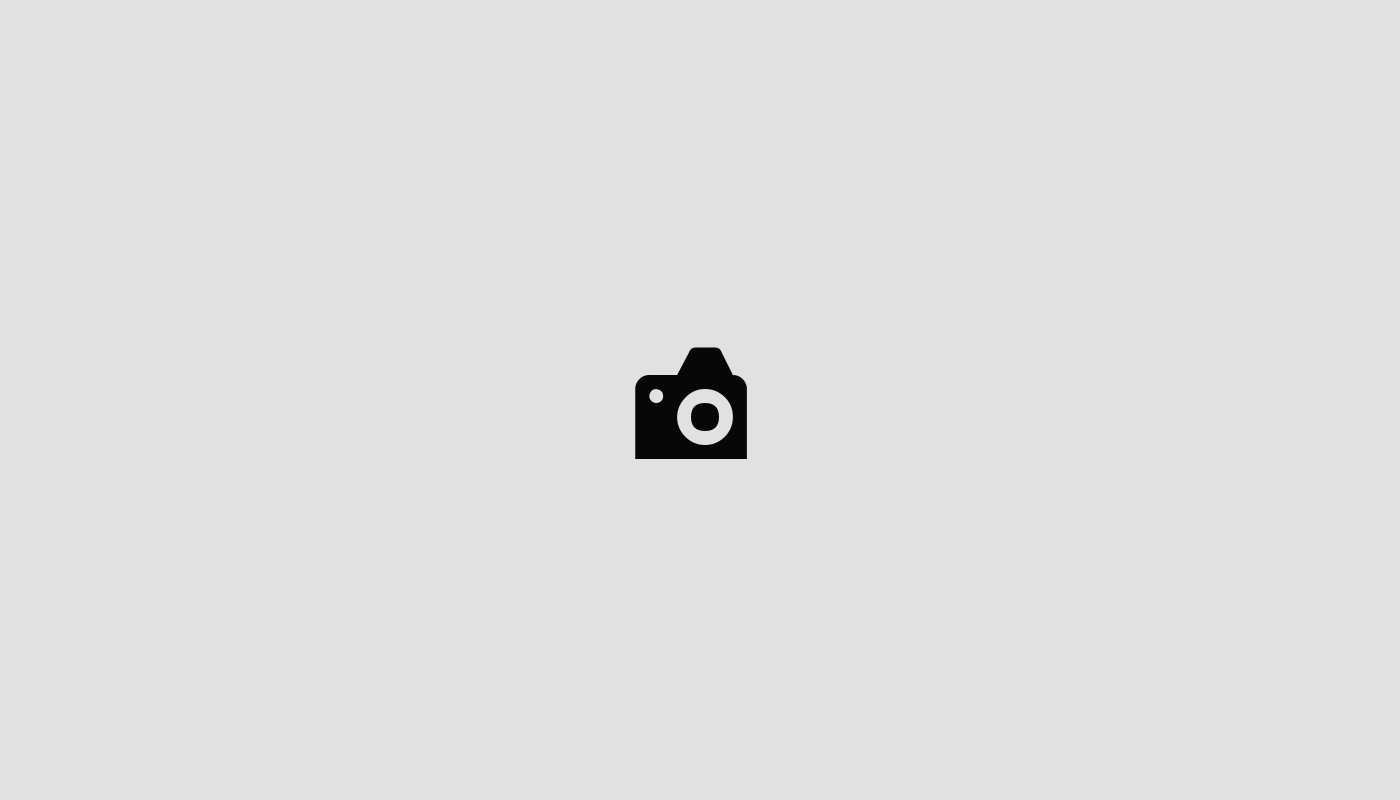
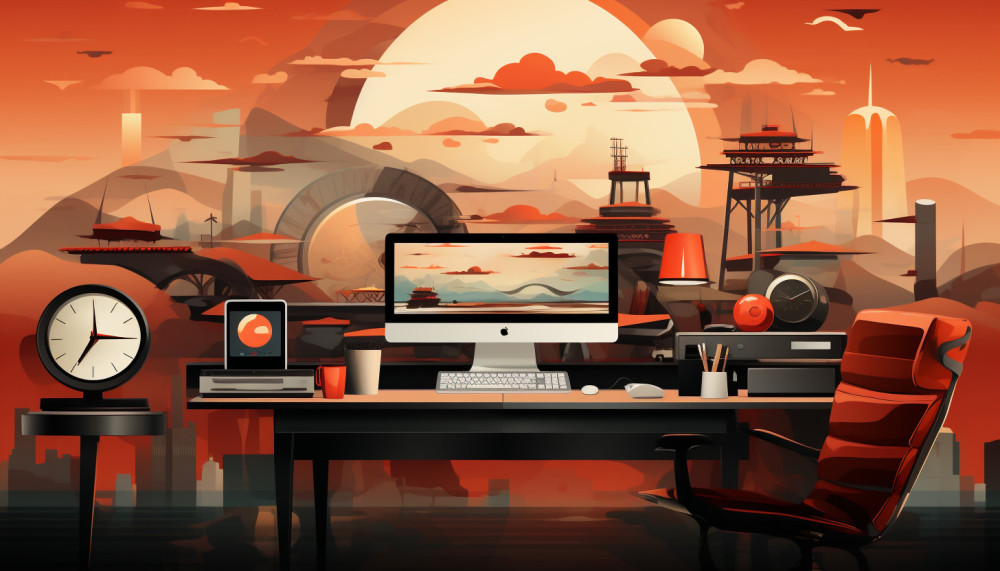
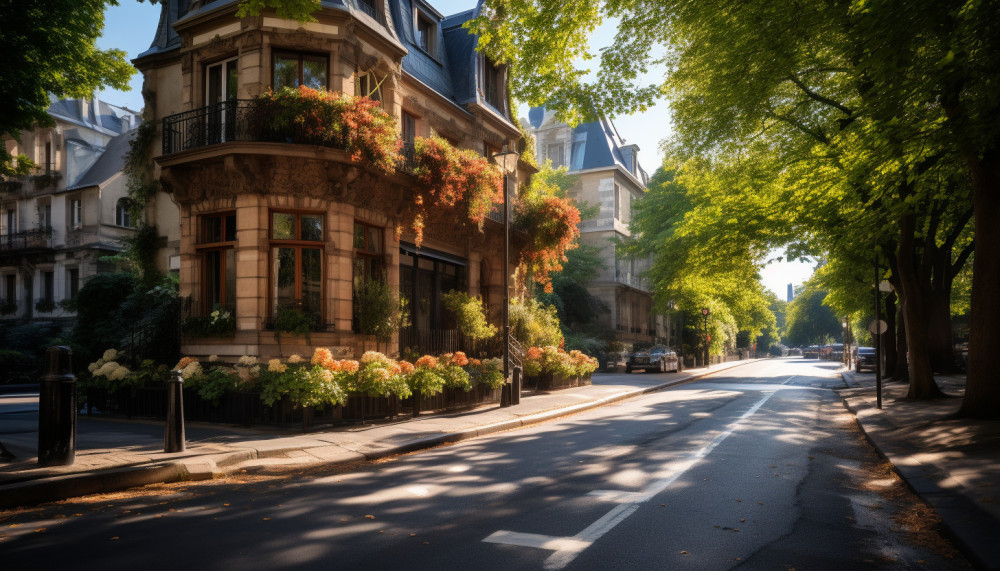
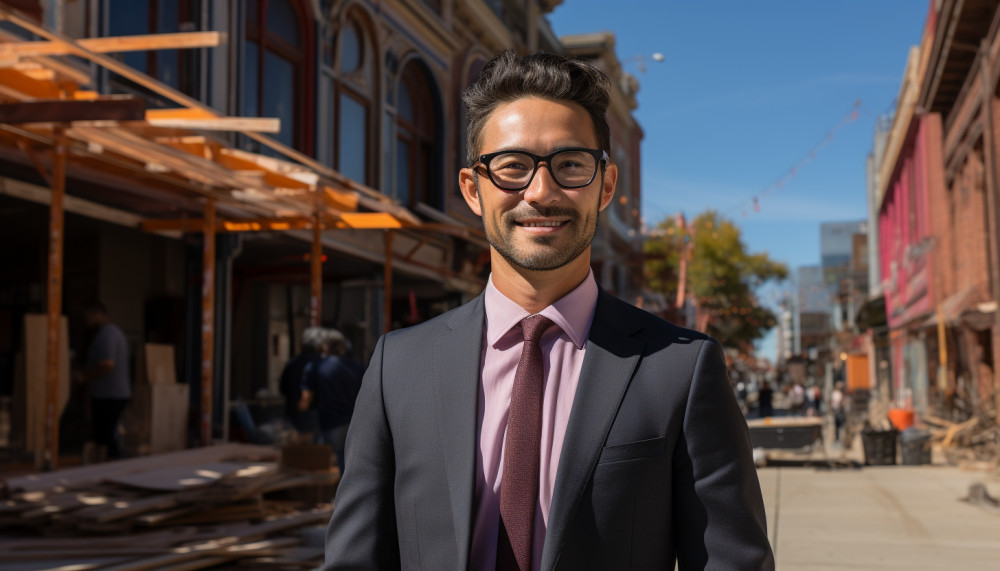
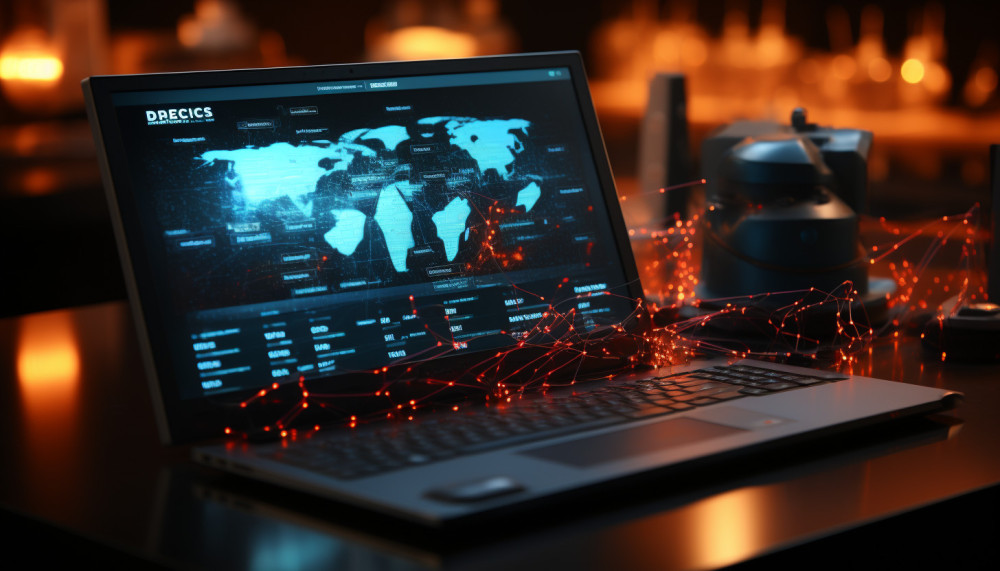
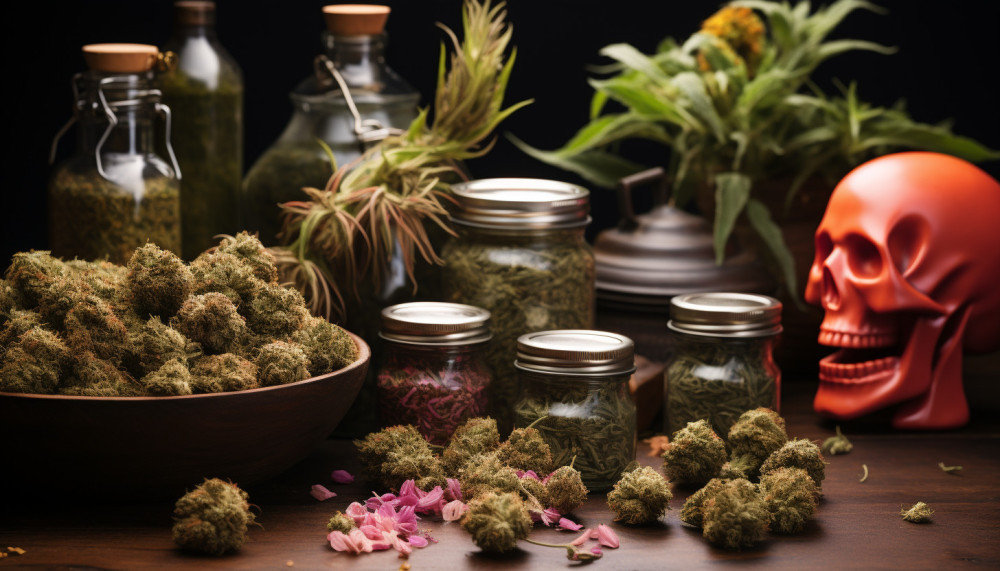
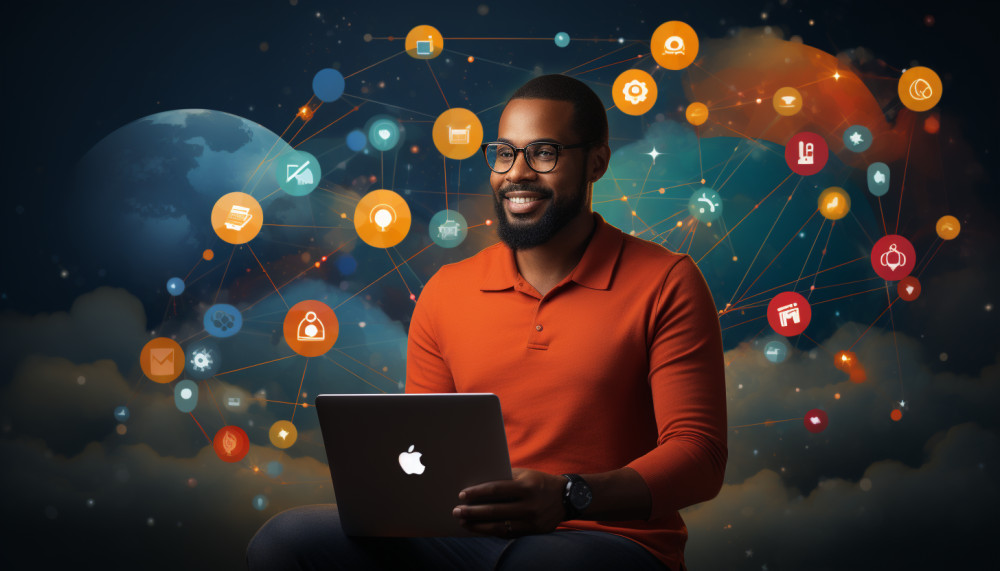
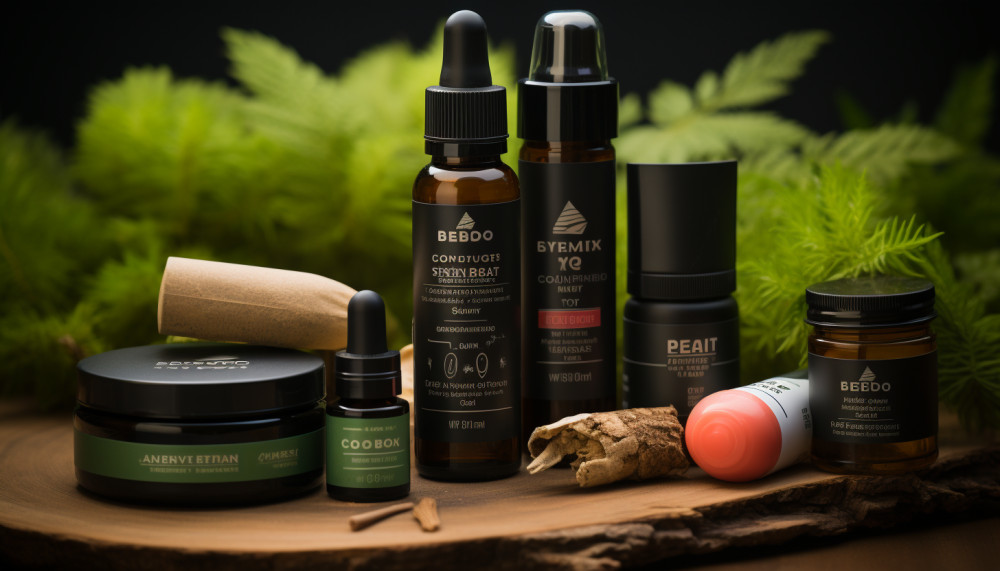
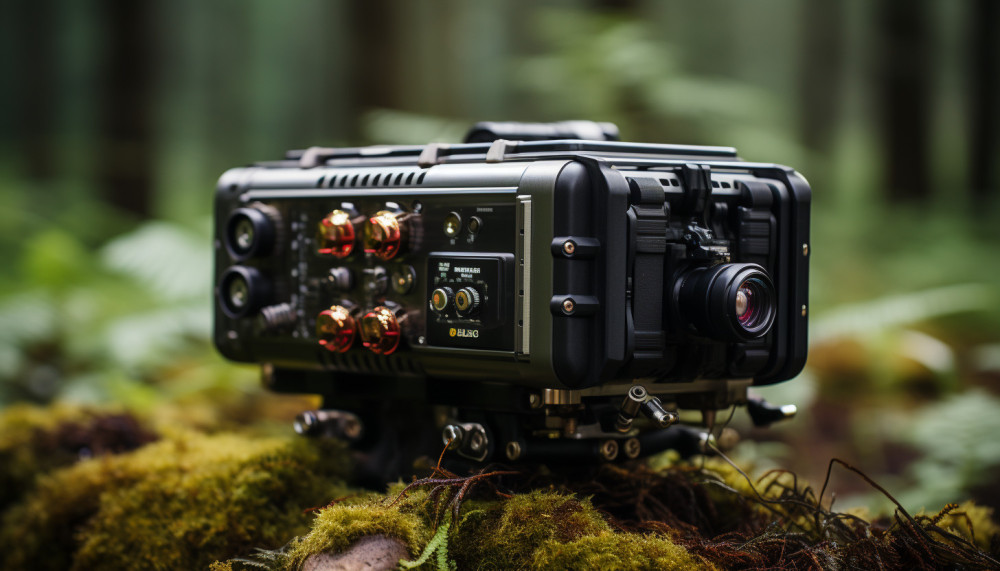
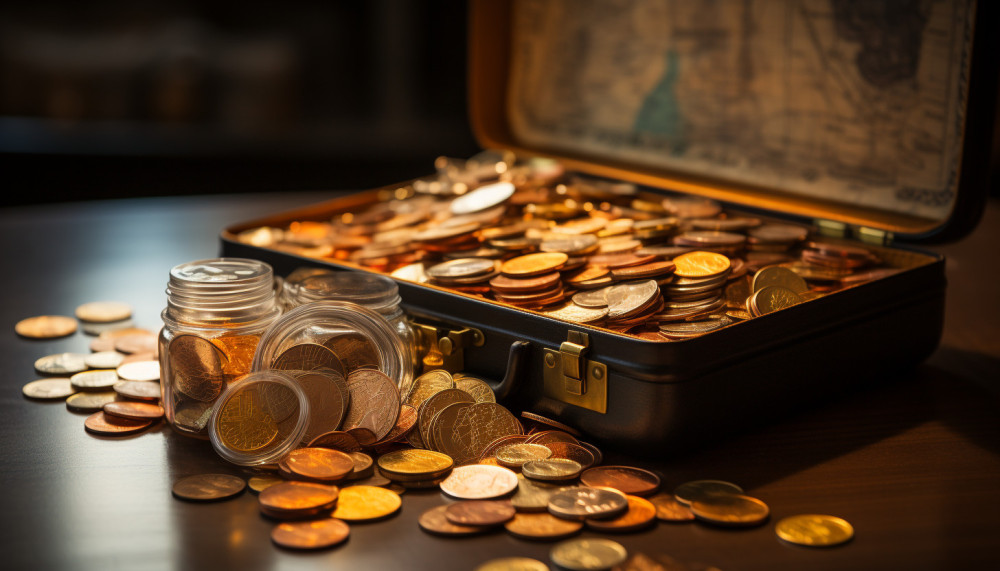
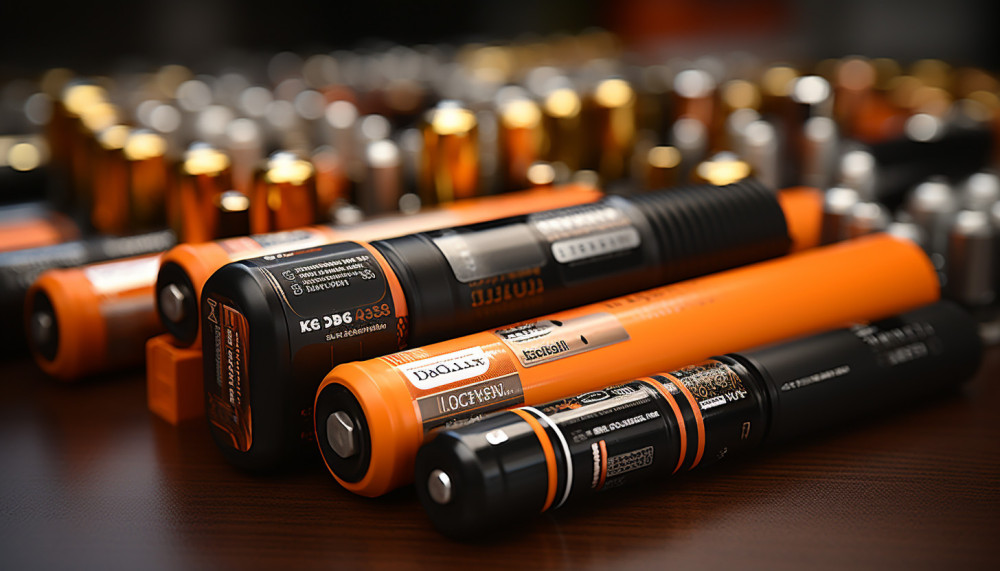
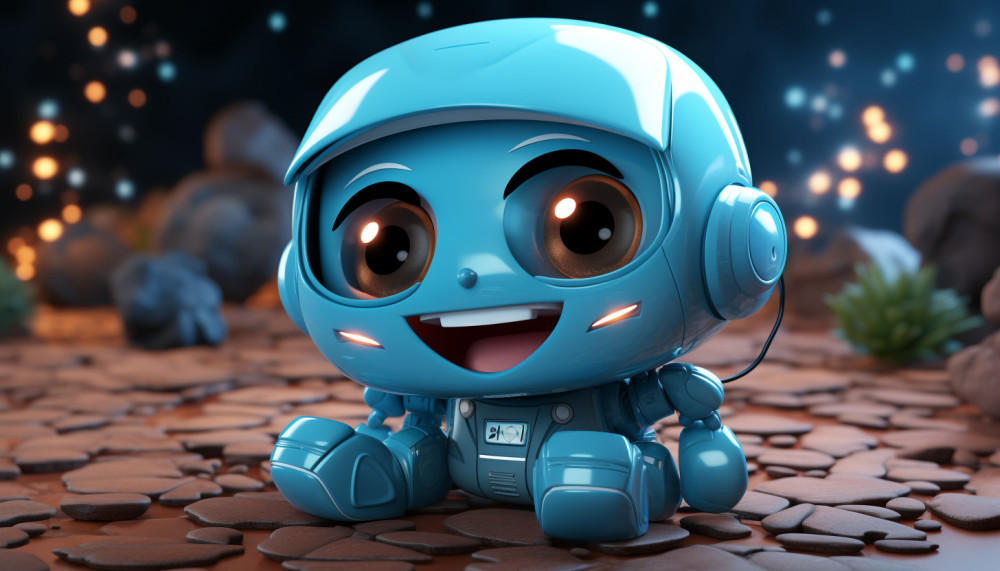
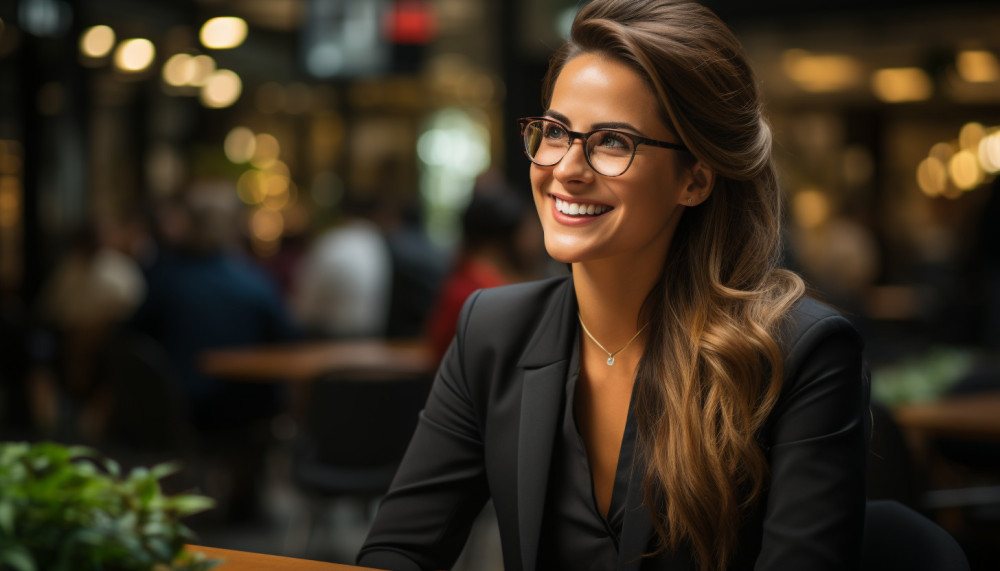
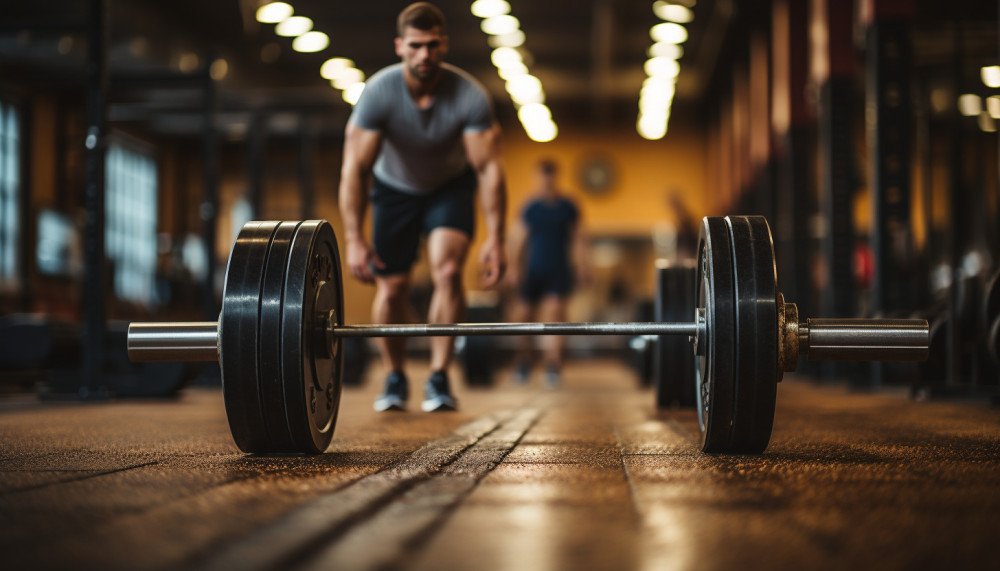
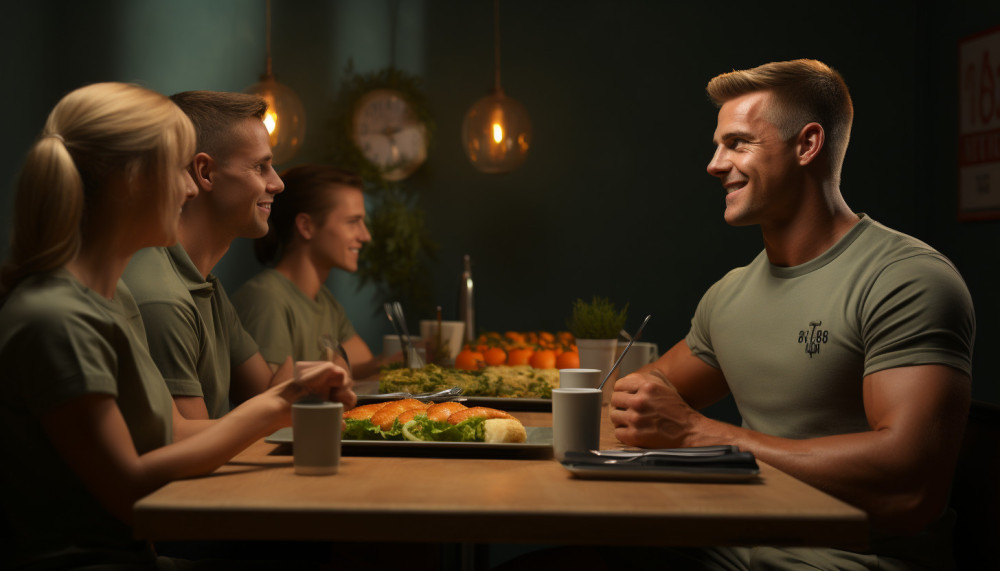
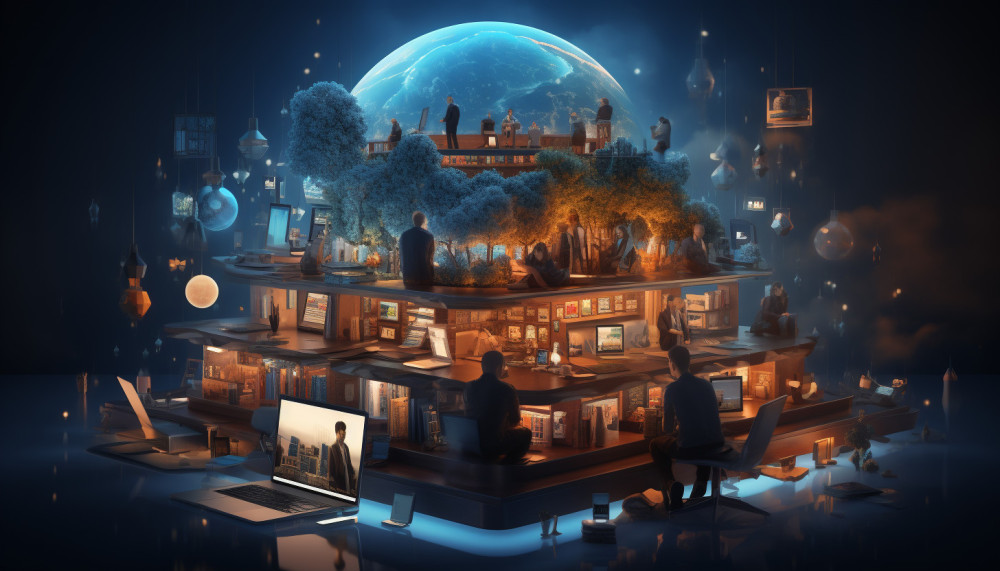
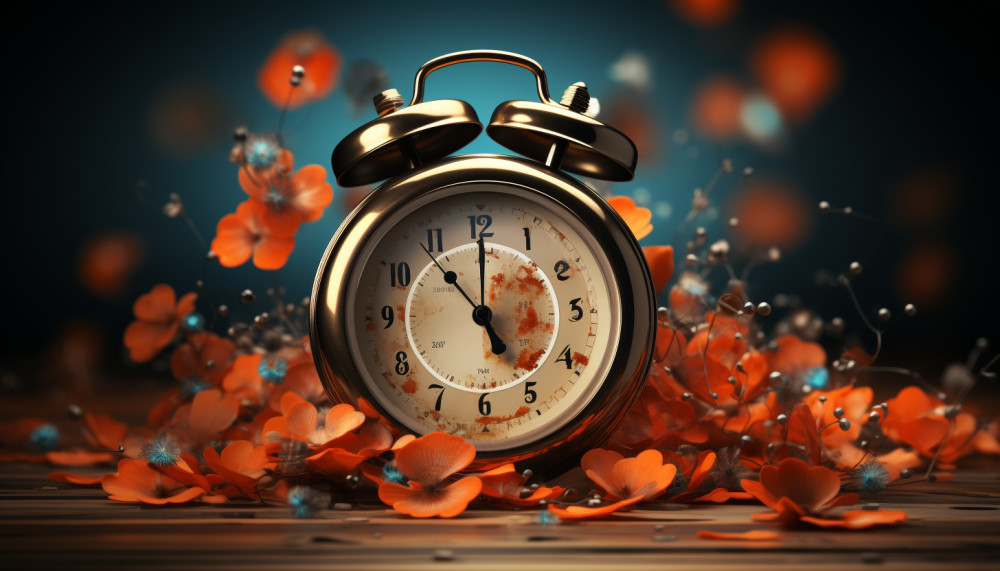
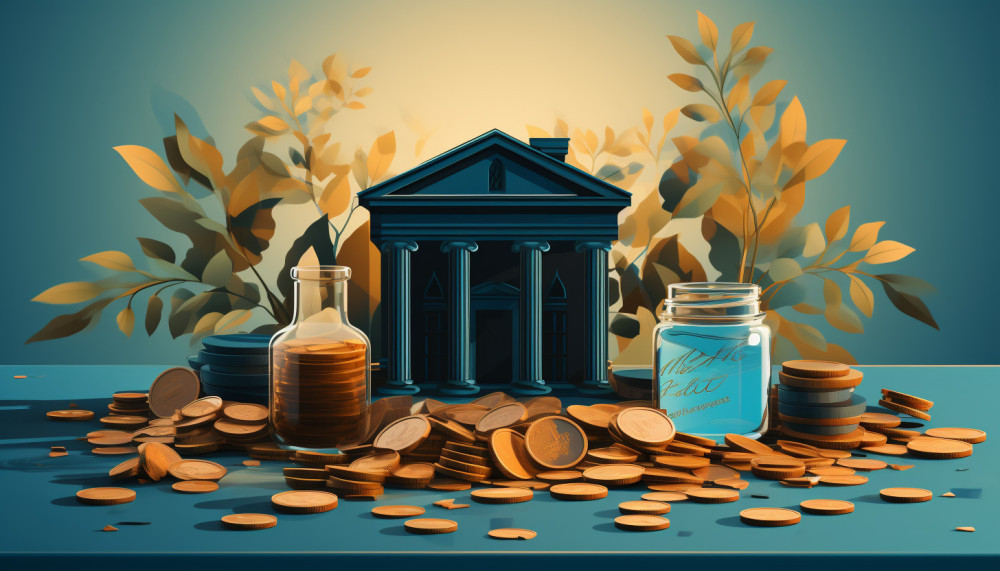
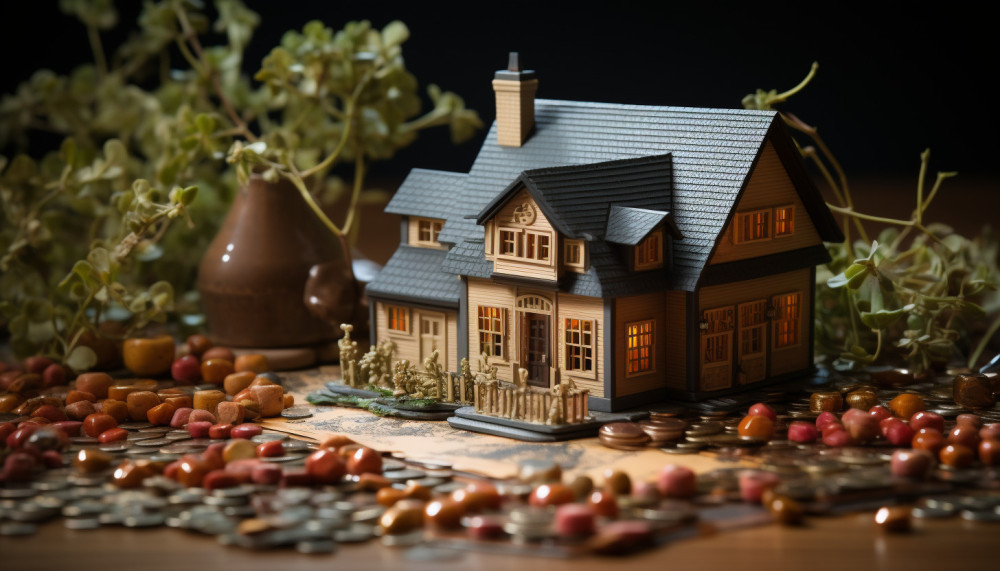
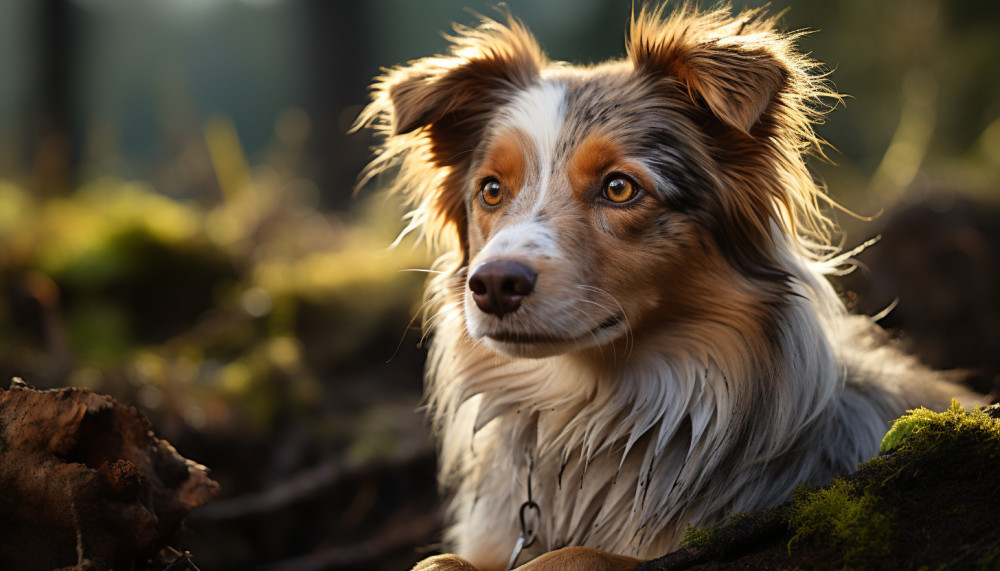